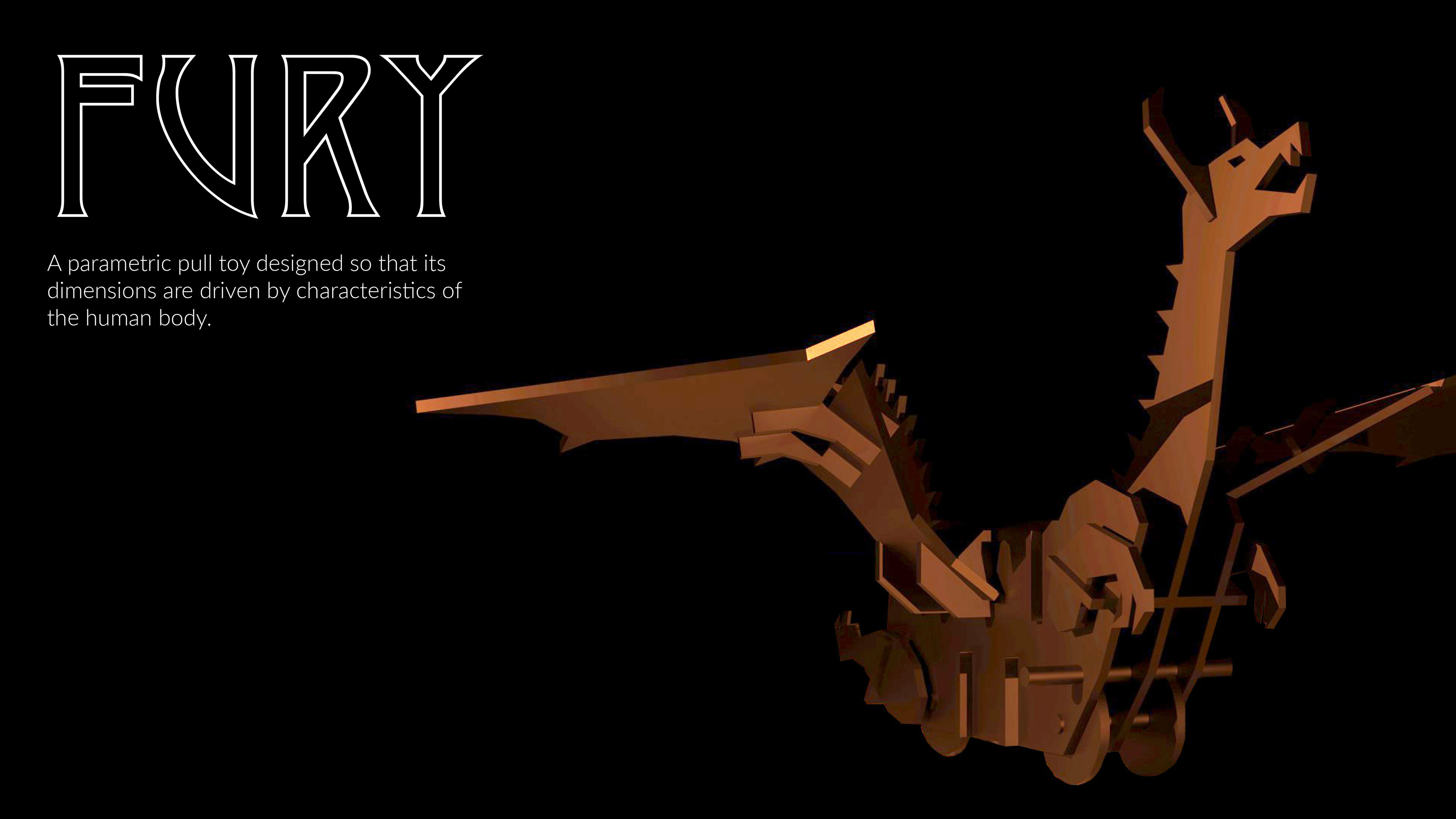
A 6-week group project dedicated to creating a product, designed around the human body, that varies in response to changes in body position and/or size. Where the body positions in the CAD file vary in at least 3 parameters from each other, fits within the material constraints of 2 sheets of 4' x 8' plywood, and at least one 3-D printed piece driven by at least two parameters. Overall, this class and project taught me how to be more efficient in 3D modeling whenever there needs to be an engineering deign change by embedding intelligence within the digital model.
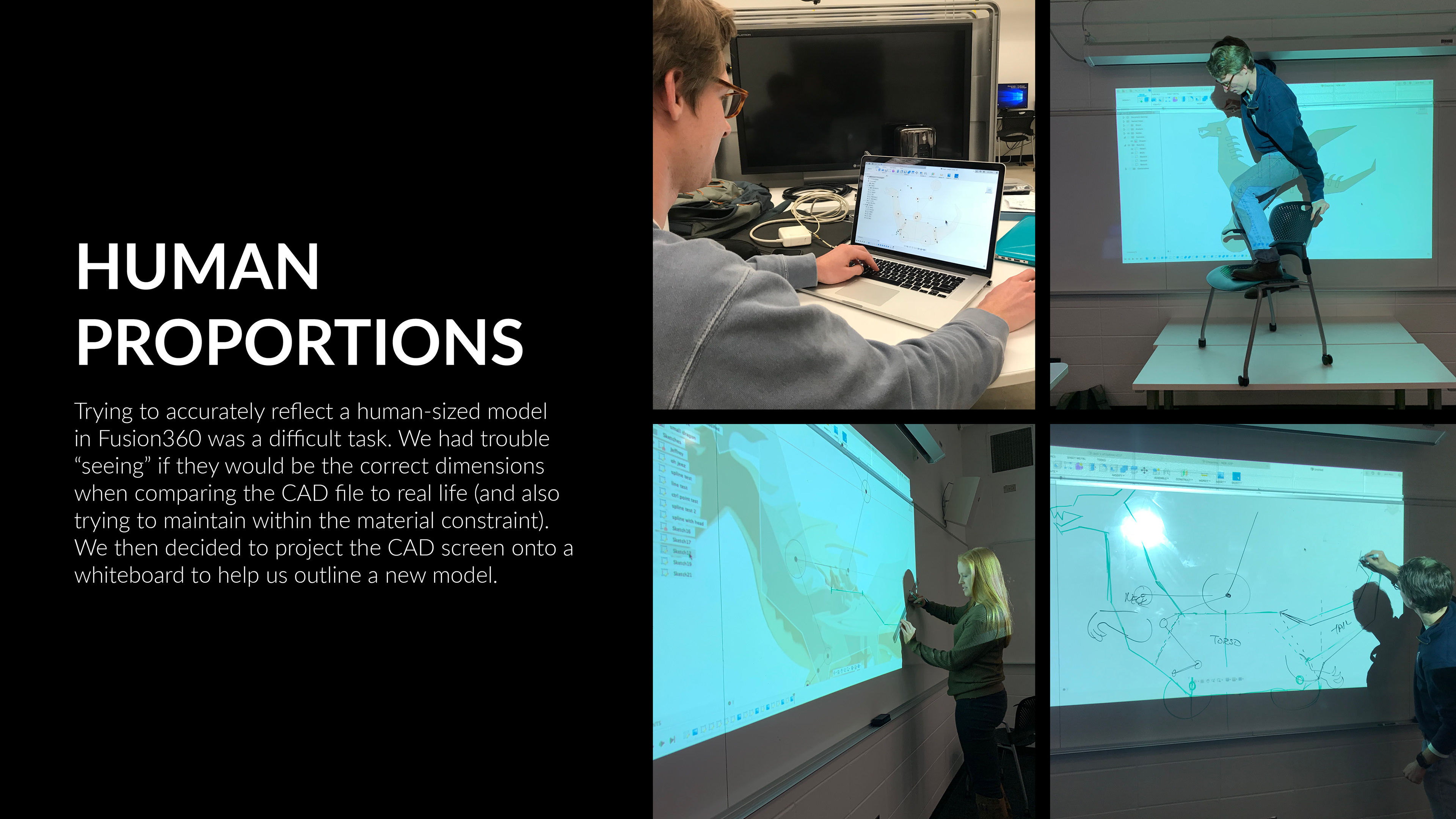
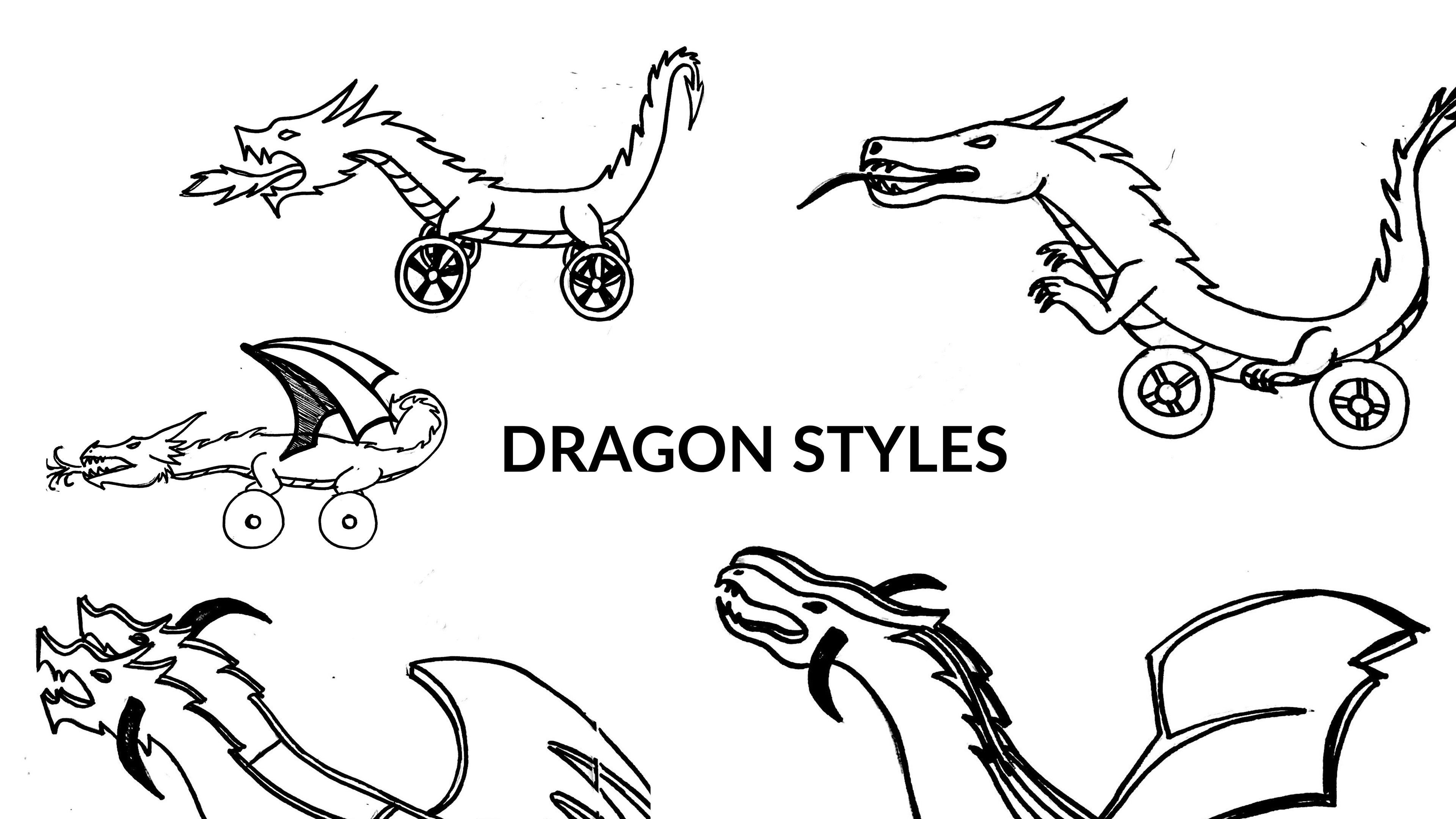
While figuring out the parameters feature in Fusion360, we were also trying to figure out what type of aesthetic we wanted to go for.
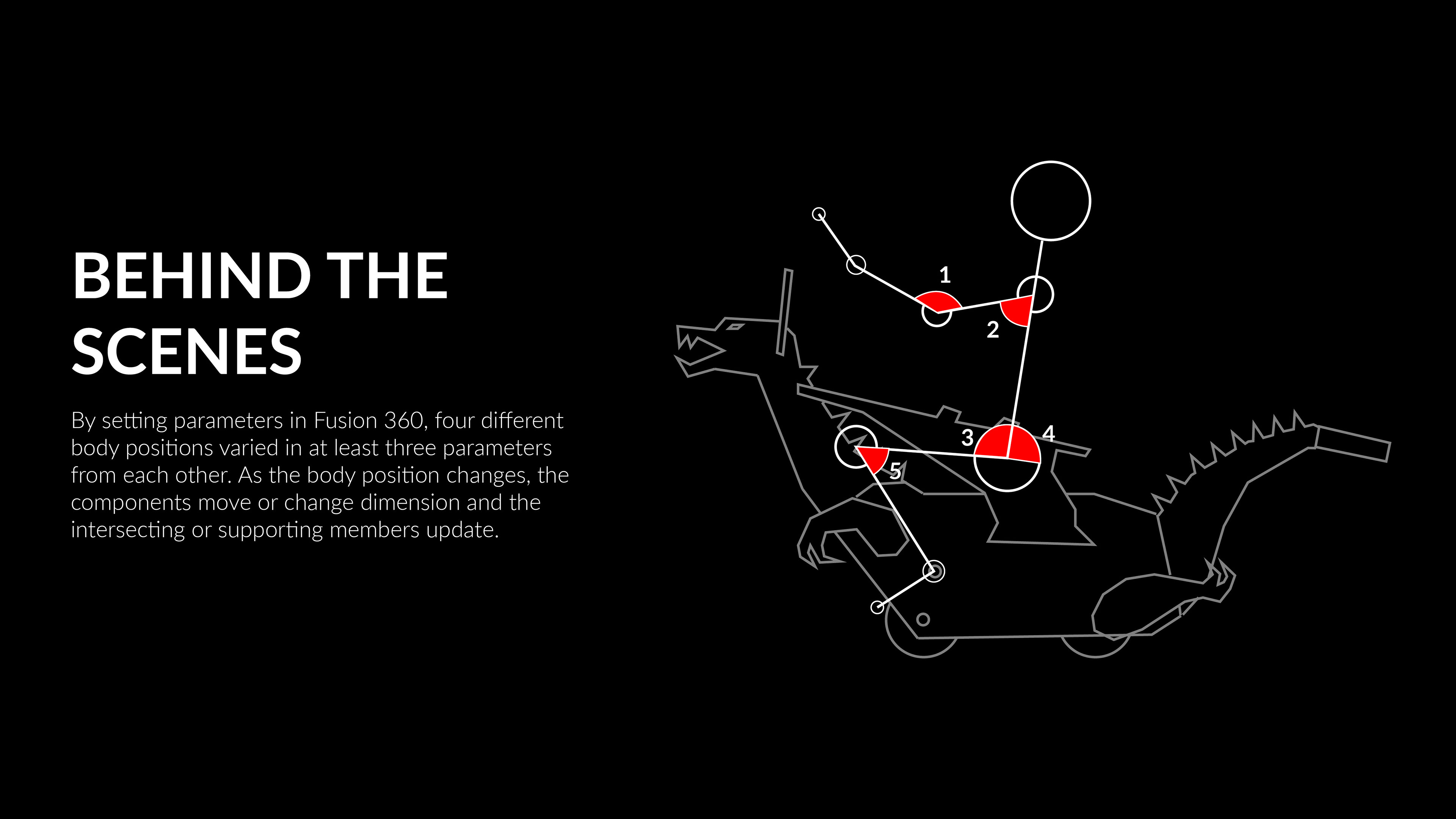

There are both internal and external relationships. The pull toy's dimensions are driven by the characteristics of the human body (external), but additionally, the relationships between components within the pull toy itself are also evident where if one component moves or changes dimension, then intersecting or supporting members also update (internal).
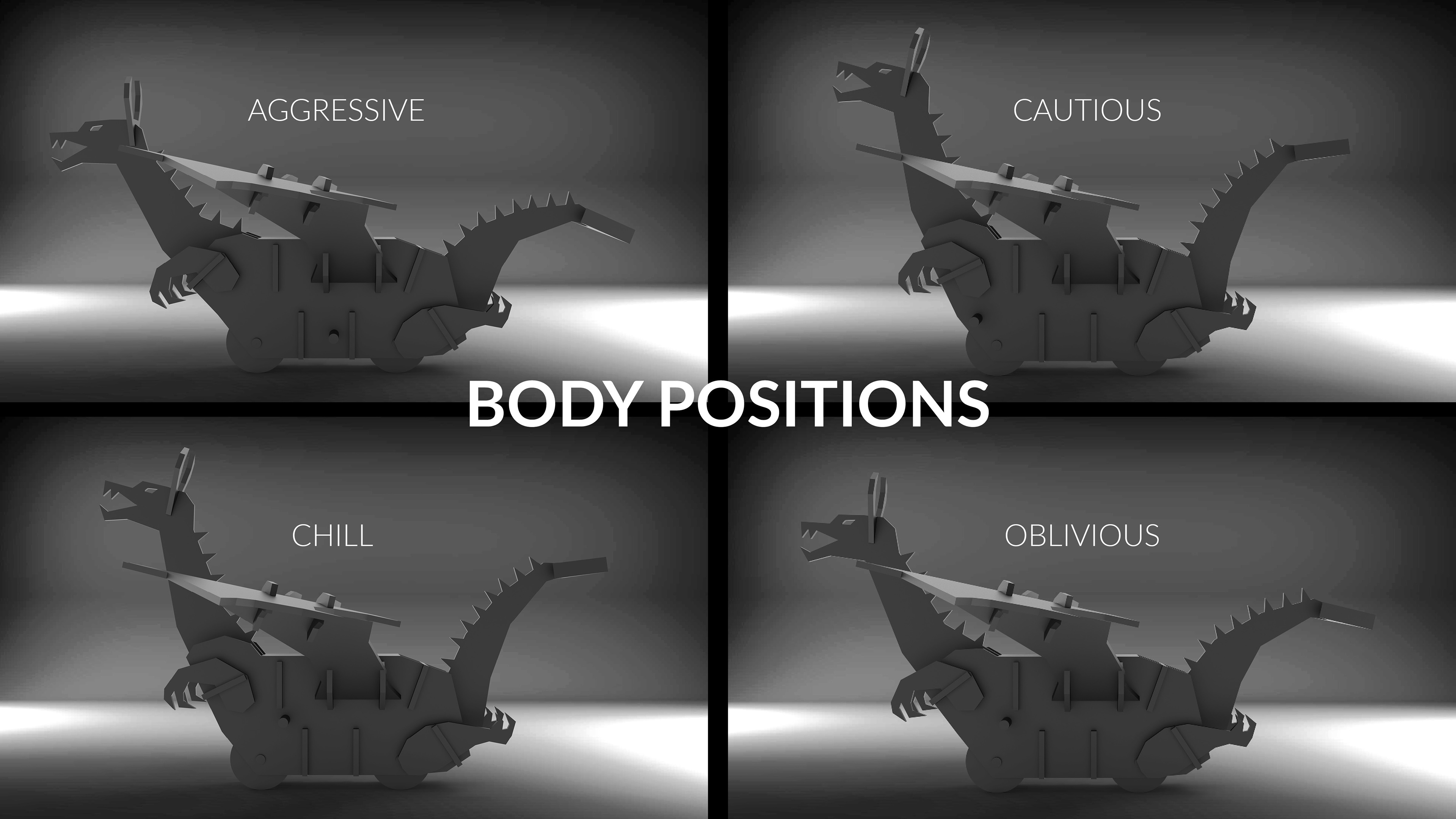
As you change the angles of the human body (angles 1-6 in previous slide), the dragon's neck, tail, head, and foot peg will also update into these four different pull toy positions.
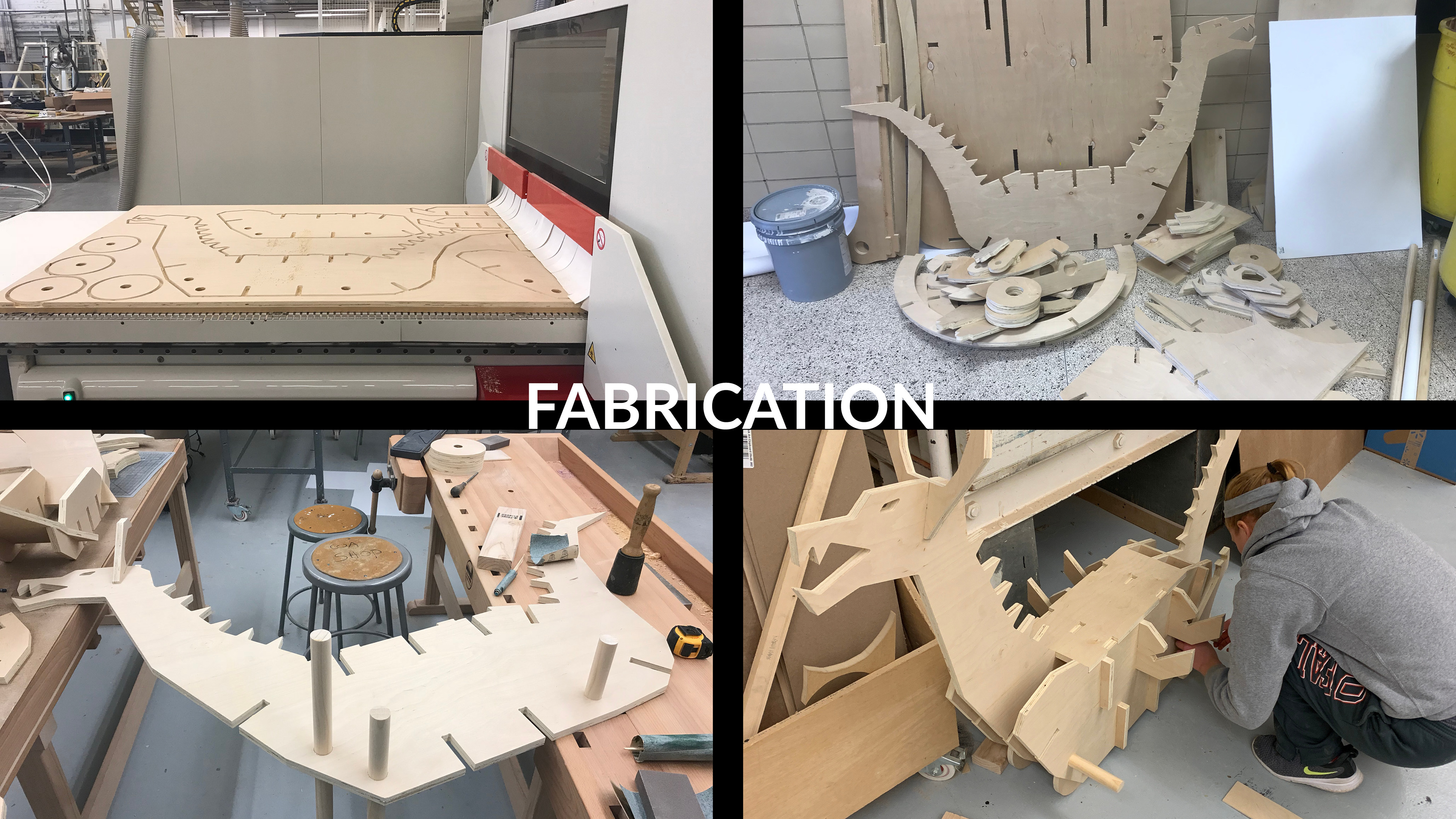
We used a 3-axis CNC to cut out each piece by using the CAM feature on the Fusion360 file with small tolerances (friction fit) to avoid having to use any nuts/bolts/screws or any glue.
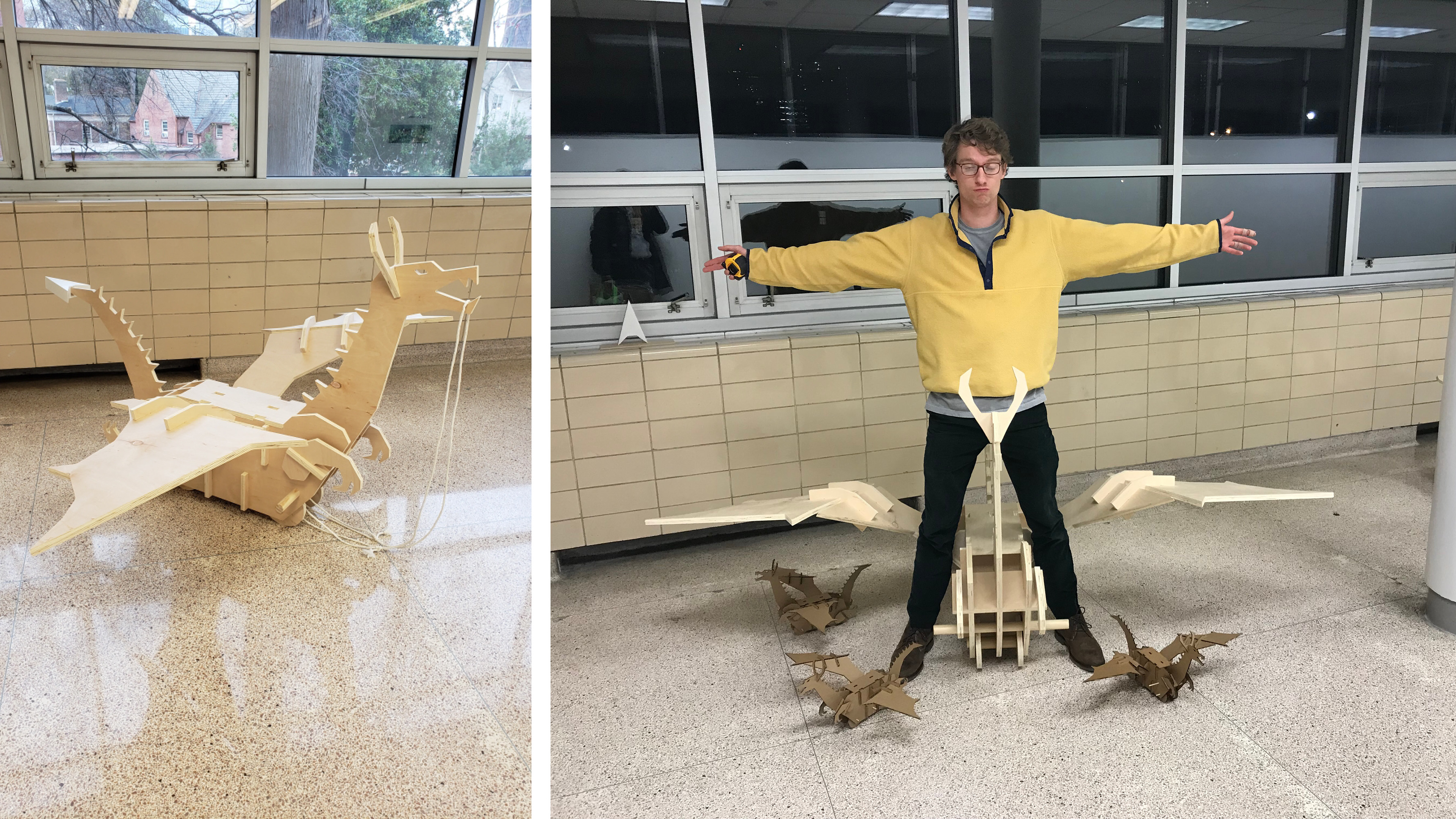
One body position was chosen and assembled. It rolls perfectly, but sadly does not fly.
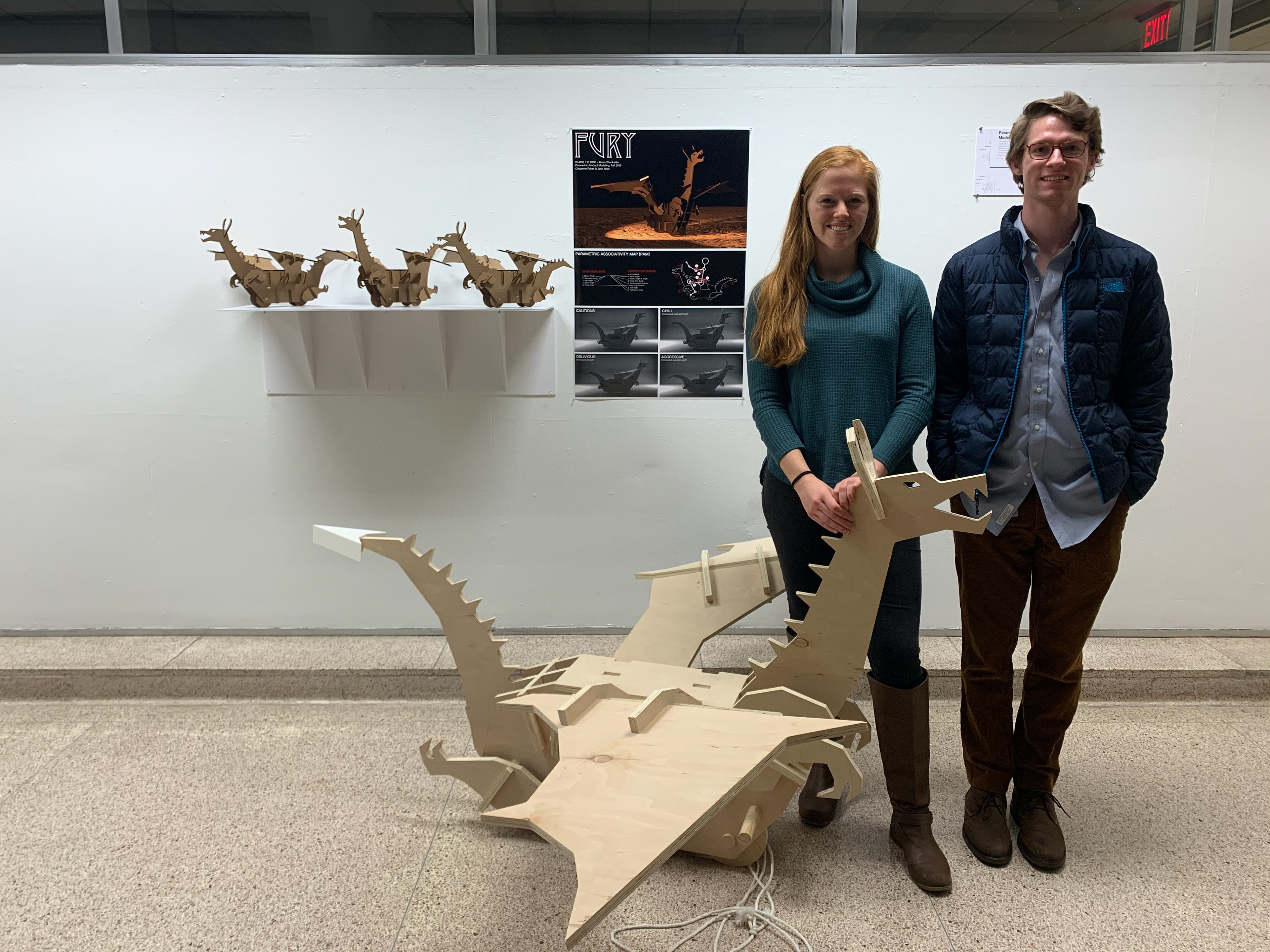
A HUGE thank you goes to Jack Walz for being my partner and his awesome attention to detail and always remaining determined to finish through to end with a great result!
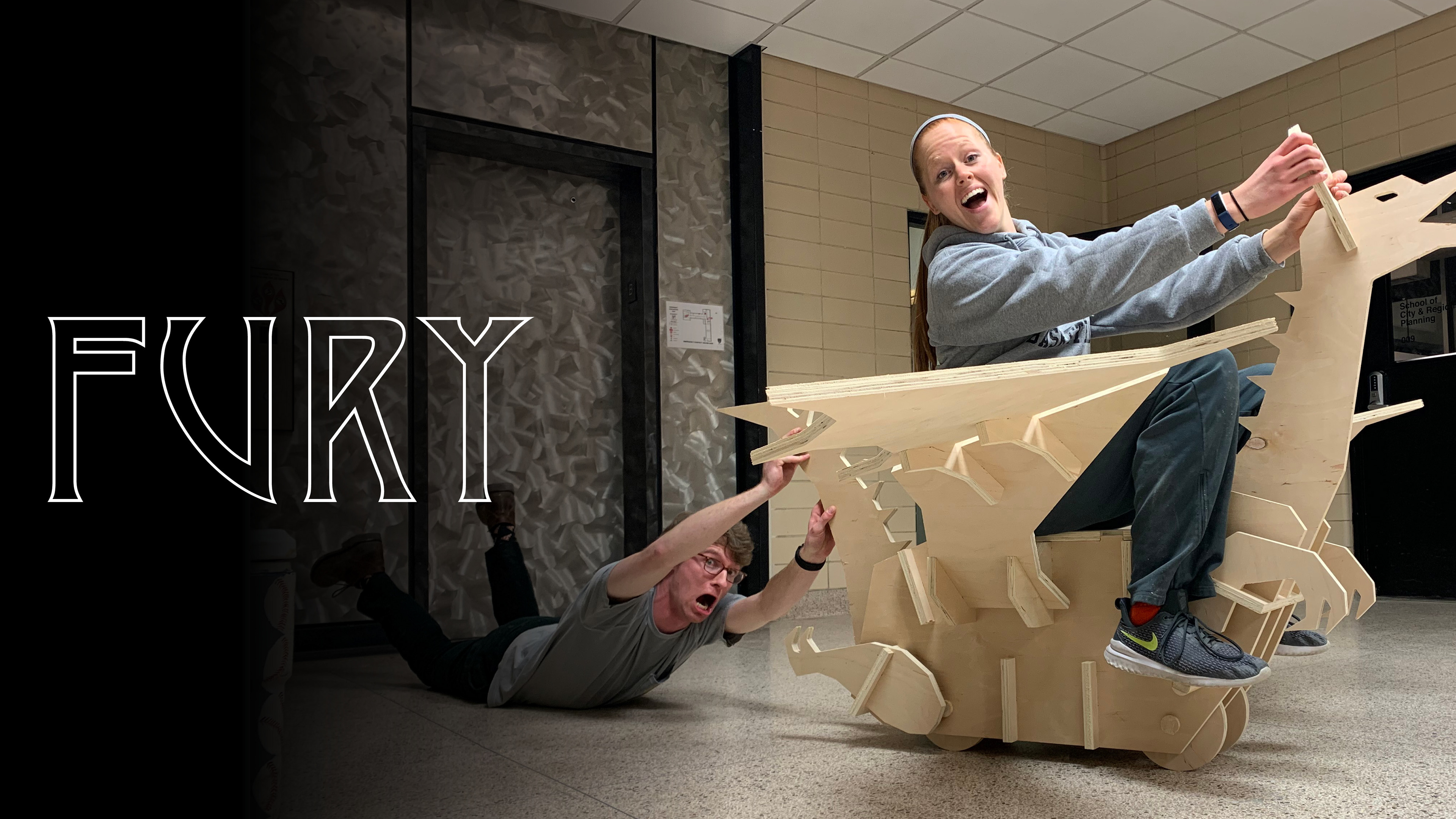
We definitely had to take a silly picture after conquering this project! (Hence the name fury haha)